Batteries are fundamental to the backup resource that a UPS provides, yet they should also be considered as one of its weakest links. They have a finite useful working life and, if left in service long enough, will eventually need replacement. Their performance and operational life can also be compromised by fault conditions arising during service.
In this article Alan Luscombe, director at KOHLER Uninterruptible Power Ltd., a KOHLER company, looks at the battery fault conditions that can arise, their causes, and how to mitigate their effects through using up to date testing and control strategies.
All uninterruptible power supplies (UPSs) depend on a reliable energy storage mechanism for accumulating electrical energy during normal mains power supply and dispensing it to the critical load if this supply fails or exceeds critical limits. Currently, this function is most frequently fulfilled using VRLA lead acid batteries. Accordingly, in this article we look at the steps UPS owners and operators should take to optimise performance and maximise life for these batteries.
Modern sealed valve-regulated lead-acid (VRLA) batteries are environmentally friendly in operation, safe, and suitable for use in office environments. Manufacturers usually design their UPS cabinets to accommodate batteries, whilst also offering matching battery cabinets or racks for when extra battery autonomy is required.
A UPS battery system for a UPS application comprises of a number of blocks that can be built up and configured to meet specific needs of individual applications. Firstly, a single series string can be assembled to meet UPS float voltage settings, as the voltage across the string’s terminals equals the sum of the individual block voltages. Then, a number of series strings can be connected in parallel, either to increase the battery Ah rating and autonomy, or to build in battery redundancy. If one series string fails, any others connected in parallel will continue to operate.
Once the battery blocks have been configured and installed into the UPS system, a regular monitoring and maintenance programme should be initiated; this is vital to combine maximum battery performance with the longest possible operational life. To understand the necessity and benefits of such a programme, we can start by looking at the problems that can afflict batteries during their working life.[/vc_column_text][vc_column_text]
Common battery problems
Many problems arise from poor equalisation, where some battery blocks may overcharge while others are undercharging.
During overcharging, excessive charge voltages force a high overcharge current into the battery. This dissipates as heat, and in a VRLA battery, may cause gas emission through the safety valve. Within a short period this will corrode the positive plate material and shorten the battery’s life. Overcharging can also lead to batteries drying out and losing charging capacity, or suffering from thermal runaway. Thermal runaway occurs when a battery generates heat more quickly than it can dissipate it. This increases internal battery temperature, dries out the cells and possibly damages or ruptures the plastic battery container.
Undercharging can result in a battery block’s terminal voltage falling below its rated value. If a battery is left in a discharged state, or stored for a prolonged period of time, lead sulphate crystals start to form, acting as a barrier to recharging and preventing normal battery operation. Depending on the degree of sulphation, a battery may be recovered by constant current charging at a higher voltage than that used for standard charging, with the current limited to one tenth of the battery capacity, for no more than 4 to 10 hours.
Note that this process involves exceeding the battery’s normal recommended charging voltage, so the battery must be monitored at all times for safety’s sake. It must be removed from charge if excessive heat is generated. The voltage required to ‘force’ the maximum current into the battery will reduce as the battery recovers until normal charging can take place. However, in some circumstances a battery may never fully recover from sulphation, and will need to be replaced.
If batteries are insufficiently monitored, an undercharged condition may further deteriorate into a state of deep discharge. A battery is considered to be deeply discharged if its on-load voltage falls below a predetermined critical level. Severe sulphation will result, and in extreme cases the battery will be unable to accept a recharge and will need replacing.
Battery operation is an electrochemical process and as such is highly temperature-dependent. Most manufacturers recommend a working temperature environment of +20°C. As temperatures start to increase, more power can be extracted from the battery. However long term exposure to a higher temperature will adversely affect the anticipated service life of a battery. The empirical equation is that for every 10 °c above the recommended ambient temperature the life would be halved.
If the ambient temperature drops below optimum, the rate of chemical reaction and therefore battery performance reduces, although reduced temperatures have little effect on battery service life. Any AC component or ’ripple’ allowed to be superimposed onto the battery’s DC charging voltage will, however, adversely affect battery life. Modern transformerless design UPS systems utilise a dc:dc converter for the battery charger thereby eliminating the possible effects of this superimposed a.c. ripple associated with legacy transformer based design UPS units.
Fig. 1: Temperature/life characteristics of a typical VRLA battery
Battery maintenance and testing
The battery maintenance schedule, once initiated, can start with some simple but important checks. These include inspecting all the battery terminals and connections for corrosion, and the batteries themselves for cracks, leaks or swelling. All intercell connections should remain tightened according to the manufacturer’s specifications, while the batteries and surrounding area should be kept clean and free of debris. Voltages across battery terminals can also be checked.
However, these checks have limitations. Voltage readings do not provide a true indication of battery condition, and VRLA batteries’ sealed, opaque cases preclude visual inspection and measurement of specific gravity as performed on earlier battery types. Accordingly, more sophisticated tests are now used to supplement the simple inspection methods described above.
The most important of these tests is based on battery impedance testing, as battery impedance can reveal much about overall health. New batteries have a fairly low internal impedance, usually measured in milliohms. This impedance increases marginally over time due to normal internal corrosion, occurring at a similar rate across batteries in a string. But this rise in impedance will become more significant in batteries that develop problems such as loss of electrolyte or excessive internal corrosion. Accordingly, impedance testing allows latent failures to be identified and removed before they become actual problems. Impedance testing can be performed without discharging or otherwise stressing the batteries.
Load bank testing also has a role as it reveals the battery’s current capacity. It proves the battery will support the specified load for the expected time. However it should be used sparingly, as it completely discharges the battery, shortening its useful life and removing it from service until it can recharge. Batteries specifically designed for UPS applications to have finite cycle life.
One of the most advanced systems for battery care is KUP.’s PowerNSURE system, which allows operators to continuously monitor and manage their UPS batteries either locally or remotely across the Internet. PowerNSURE checks the key parameters – internal resistance, voltage and temperature – for each individual battery block . Battery status is then reported, together with warnings if attention is required. Fig. 2 shows a PowerNSURE graphical report of a battery fault.
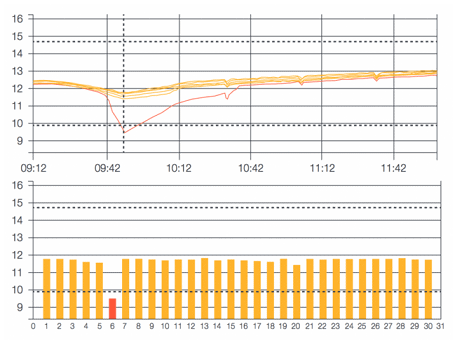
Fig. 2: PowerNSURE graphical report – showing Battery 6 is weak after 35 minutes of discharge
Fig. 2: PowerNSURE graphical report – showing Battery 6 is weak after 35 minutes of discharge
In addition to monitoring, PowerNSURE runs an equalisation process, constantly controlling the charging voltages for each battery; this prevents undercharging and overcharging, extending the life of the battery and guaranteeing its availability at all times.
Conclusion
Lead-acid batteries in their modern VRLA format provide the best available backup power solution for most commercial UPS applications. They are, however, vulnerable to misuse and excessive ambient temperatures and in any case have a finite operating life. A well-designed monitoring and control regime is accordingly essential to ensuring their maximal operational life and performance.
Published in April 2016 edition of Electrical Review & May 2016 edition of PBSI
Follow us on LinkedIn for regular industry articles & company information